SPC Glossary: P, Q, R
Your quick reference to statistical process control for manufacturing quality management systems.
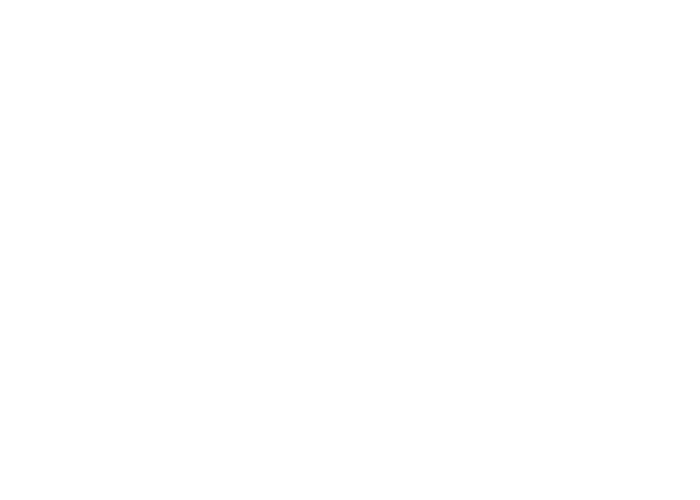
SPC DEMO
Don’t miss out! Book a demo of our specialized SPC software and unlock immediate improvements in your processes.
Quality Management System Glossary: P, Q, R
P
Pareto Chart
Also known as the 80-20 rule.
A graphical tool for ranking causes from most significant to least significant. It is based on the Pareto principle, named after 19th century economist Vilfredo Pareto, and suggests that most effects come from relatively few causes; that is, 80% of the effects come from 20% of the possible causes.
Parts Per Million (PPM)
A metric reporting the number of defects normalized to a population of one million for ease of comparison.
Parts per Thousand (PPT)
A ratio often used to refer to the concentration of solutes in solutions, such as salts in water (i.e., salinity).
P Chart
See Percent Chart.
Percent Chart
Also referred to as a proportion chart.
A control chart for evaluating the stability of a process in terms of the percentage of the total number of units in a sample in which an event of a given classification occurs.
Percentiles
Percentiles divide the ordered data into 100 equal groups. The kth percentile pk is a value such that at least k% of the observations are at or below this value and (100-k)% of the observations are at or above this value.
Plan-Do-Check-Act (PDCA) Cycle
Also known as PDCA Model.
A four-step process for quality improvement. In the first step (plan), a way to effect improvement is developed. In the second step (do), the plan is carried out. In the third step (check), a study takes place between what was predicted and what was observed in the previous step. In the last step (act), action should be taken to correct or improve the process.
Poisson Distribution
A discrete probability distribution that expresses the probability of a number of events occurring in a fixed time period if these events occur with a known average rate and are independent of the time since the last event.
Precision
The amount of variation that exists in the values of multiple measurements of the same characteristic or parameter. Greater precision means less variation between measurements.
Probability (statistical)
The likelihood of occurrence of an event, action, or item.
Process
A set of interrelated work activities that transform inputs into outputs.
Process Average Quality
Expected or average value of process quality.
Process Capability
A statistical measure of the inherent process variability of a given characteristic.
Process Capability Index
The value of the tolerance specified for the characteristic divided by the process capability. The several types of process capability indexes include the widely used Cpk and Cp.
Process Control
The method for ensuring that a process meets specified requirements.
Process Improvement
Actions taken to increase the effectiveness or efficiency of a process in meeting specified requirements.
Proportion Chart
See Percent Chart.
Q
Quality
A subjective term for which each person or sector has its own definition. In technical usage, quality can have two meanings: 1) the characteristics of a product or service that bear on its ability to satisfy stated or implied needs; 2) a product or service free of deficiencies. According to Joseph Juran, quality means “fitness for use;” according to Philip Crosby, it means “conformance to requirements.”
Quality Assurance/Quality Control (QA/QC)
Quality assurance is all the planned and systematic activities implemented within the quality system that can be demonstrated to provide confidence that a product or service will fulfill requirements for quality. Quality control is comprised of the operational techniques and activities used to fulfill requirements for quality. Quality Assurance and Quality Control are often used interchangeably, referring to the actions performed to ensure the quality of a product, service, or process.
Quality of Conformance
The ability of a product, service, or process to meet its design specifications. Design specifications are an interpretation of what the customer needs.
Quality Rate
See First Pass Yield.
Quartile
Quartiles divide the ordered data into 4 equal groups. The second quartile (Q2) is the median of the data.
R
Random Cause
A cause of variation due to chance and not assignable to any factor.
Random Sampling
A commonly used sampling technique in which sample units are selected so all combinations of n units under consideration have an equal chance of being selected as the sample.
Range (statistical)
The measure of dispersion in a data set (the difference between the highest and lowest values).
Range Chart (R Chart)
Also known as Range Control Chart.
A control chart in which the range (R) of a subgroup is used to track instantaneous variations and to evaluate the stability of the variability within a process.
Regression Analysis
A set of statistical processes for estimating the relationships among variables.
Rejection Number
The smallest number of defectives (or defects) in the sample or samples under consideration that will require rejection of the lot.
Repeatability
The variation in measurements obtained when one measurement device is used several times by the same person to measure the same characteristic on the same product.
Reproducibility
The variation in measurements made by different people using the same measuring device to measure the same characteristic on the same product.
Root Cause
A factor that caused a nonconformity and should be addressed with corrective action.
Root Cause Analysis
The method of identifying the initiating cause of a problem, which leads to preventing it from occurring again.
Run
A consecutive number of points consistently increasing or decreasing. A run can be evidence of the existence of special causes of variation that should be investigated.
Run Chart
A chart showing a line connecting numerous data points collected from a process running over time.