Costs of a Real-Time SPC Solution
Many manufacturers worry about the cost of implementing a real-time statistical process control (SPC) solution. But a robust solution like InfinityQS® Enact® offers a fast, impressive return on investment (ROI) by reducing costs and saving resources at a level that many companies can’t even imagine. These savings are realized in all areas of operations and quality SPC, from data collection and analysis to reporting and communications.
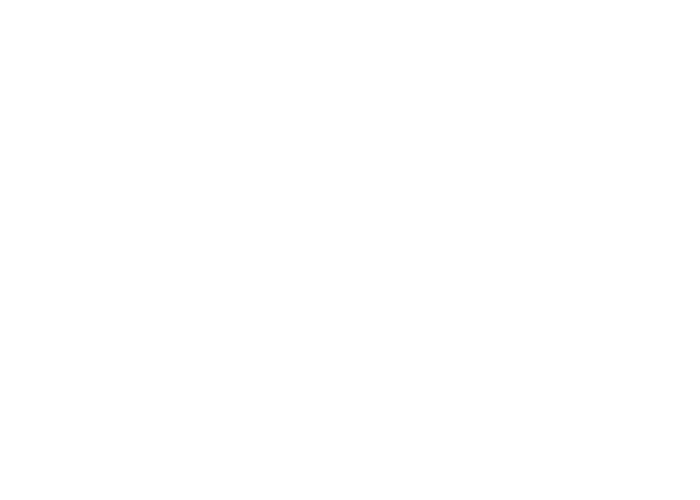
SPC DEMO
Don’t miss out! Book a demo of our specialized SPC software and unlock immediate improvements in your processes.
Manufacturing Data Collection
How much time do your operators spend manually collecting data? Many manufacturers still use paper and pencil to keep track of process quality metrics, draining resources as well as complicating future analysis and reporting. When calculating ROI for InfinityQS SPC solutions, consider how much the following factors cost you now:
- Operator time spent on manual data collection and data recording or entry
- Missed or inaccurate collections and entries
- Missed information because of data overload (lack of filtering capabilities)
Manufacturing Data Analysis
Can your quality team spot the sorts of historical trends that can lead to major cost savings? Can they compare process or product information across machines, shifts, and sites? Or do they spend countless hours trying to manipulate quality data in Excel or Minitab, simply to get the most basic results? How much do you spend in time and quality or IT resources on the following:
- Trying (or failing) to evaluate which processes, equipment, or shifts to prioritize for improvement
- Searching for additional cost savings
- Worrying about how to bring your poorest performing sites or lines up to the standard of your best performers
Manufacturing Data Reporting
When your operations team is finished with your SPC data, what happens to it? How difficult and disruptive are customer information requests or audit notifications? Without the type of true Unified Data Repository that InfinityQS solutions provide, reporting and communications can drain IT and quality resources. But with Enact, you can be assured that everyone on every team—operations, quality, IT, and executive—benefit from smoother, faster data access:
- Everyone has access to the same information, without manual, complex reporting.
- Cloud-based SPC solutions enable fully mobile, anywhere/anytime access.
- Pulling data and reports in response to audits and customer requests takes a fraction of the time required with other SPC solutions.
Focus on Priorities
Data overload is the downside of modern manufacturing.
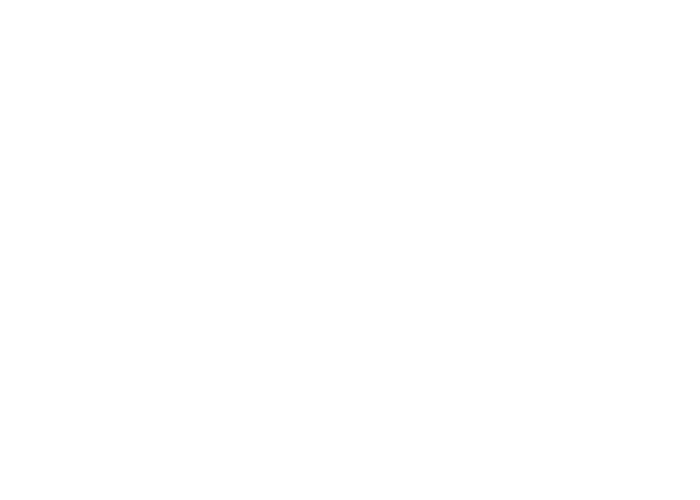
SPC DEMO
Don’t miss out! Book a demo of our specialized SPC software and unlock immediate improvements in your processes.
How SPC Can Help
With today’s Industry 4.0 manufacturing environment becoming increasingly automated and Internet-connected, operators and quality personnel alike are finding themselves swamped with data—not all of which is applicable to the task at hand. Digging through this mountain of information can eat up valuable time and increase the possibility that you’ll miss an important notification or trend. Ideally, a statistical process control (SPC) solution can help you cut through the noise, with the ability to set collection alerts and query data.
Use Enact to Focus on Top Priorities
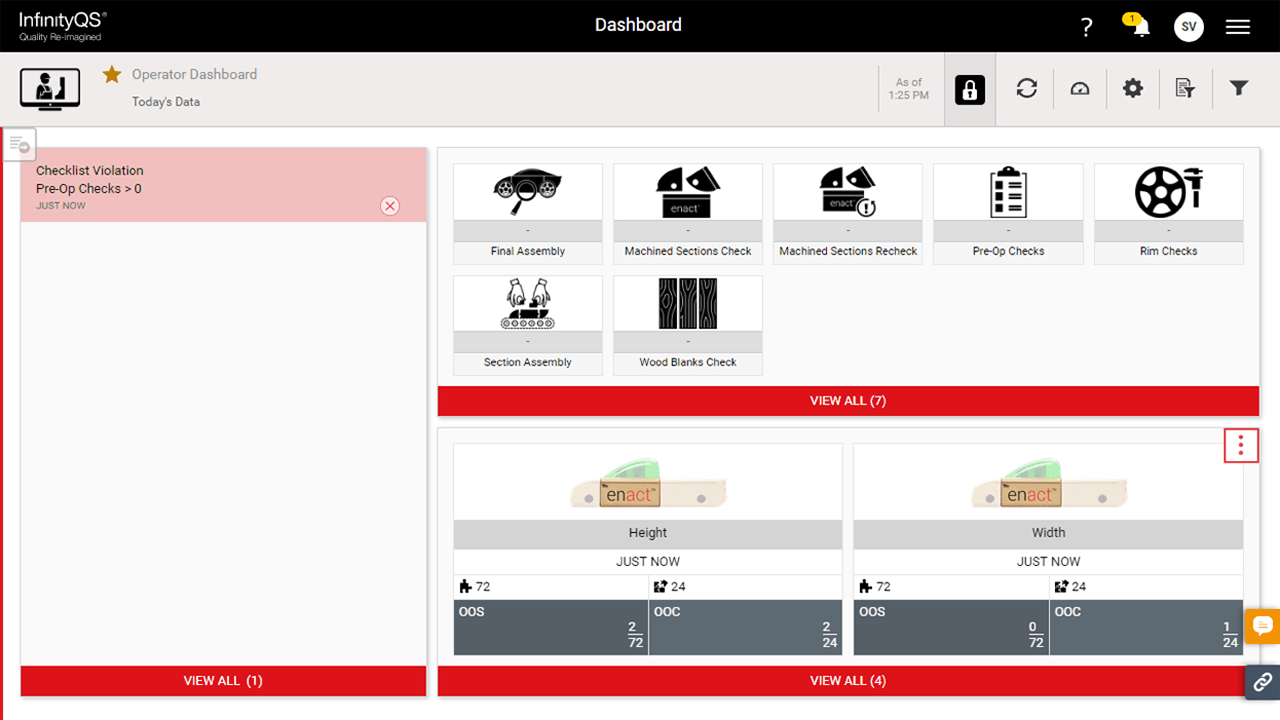
Big data can be a big headache when you’re trying to keep note of just a few priorities. That’s why Enact® uses standard (yet customizable) role-based dashboards to make your most important data easier to spot. Include the information tiles that matter most to you, based on your role, shift, and more.
An overload of quality data doesn’t organically translate into strategic insight and product improvements. A pile of Excel spreadsheets can’t compare to Enact’s intuitive data filtering, flexible notifications, and sleek dashboard tiles that give you a quick snapshot of where your process quality stands. Of course, you can dig deeper into the details with just a few clicks.
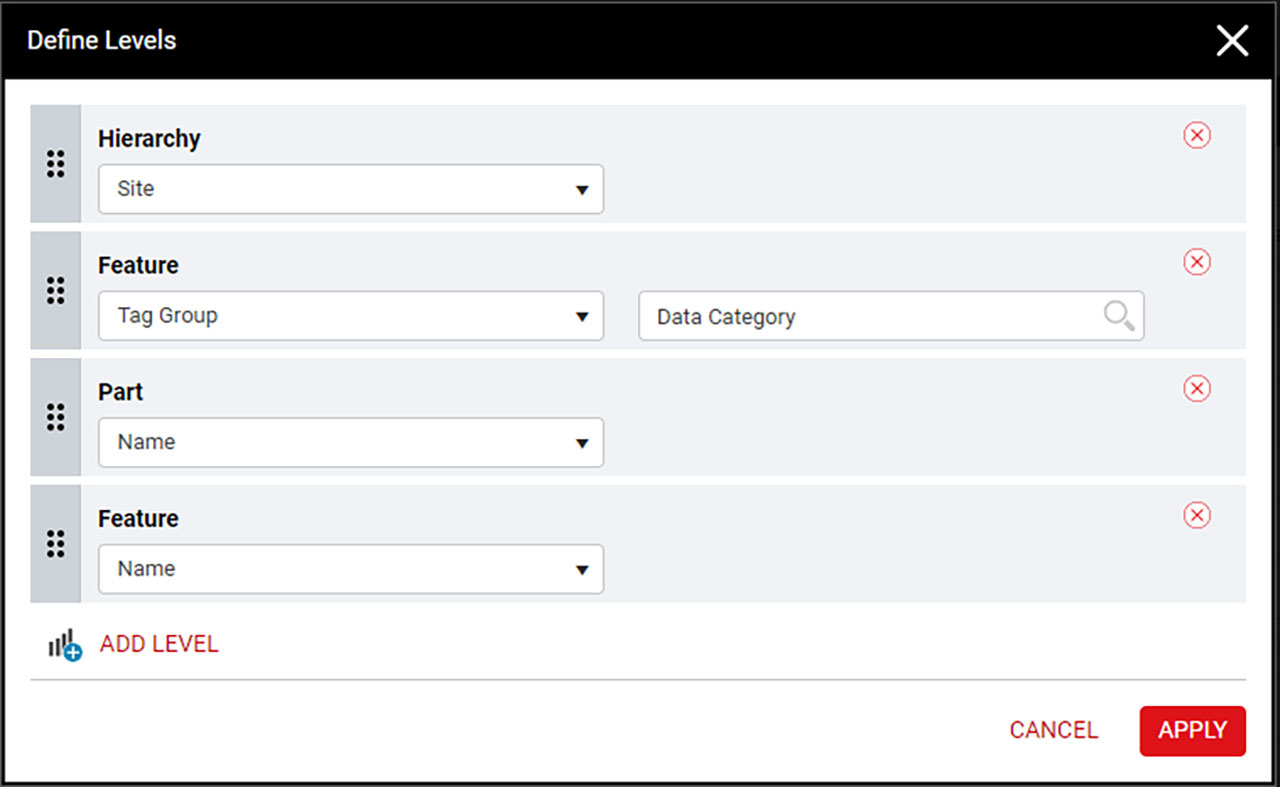
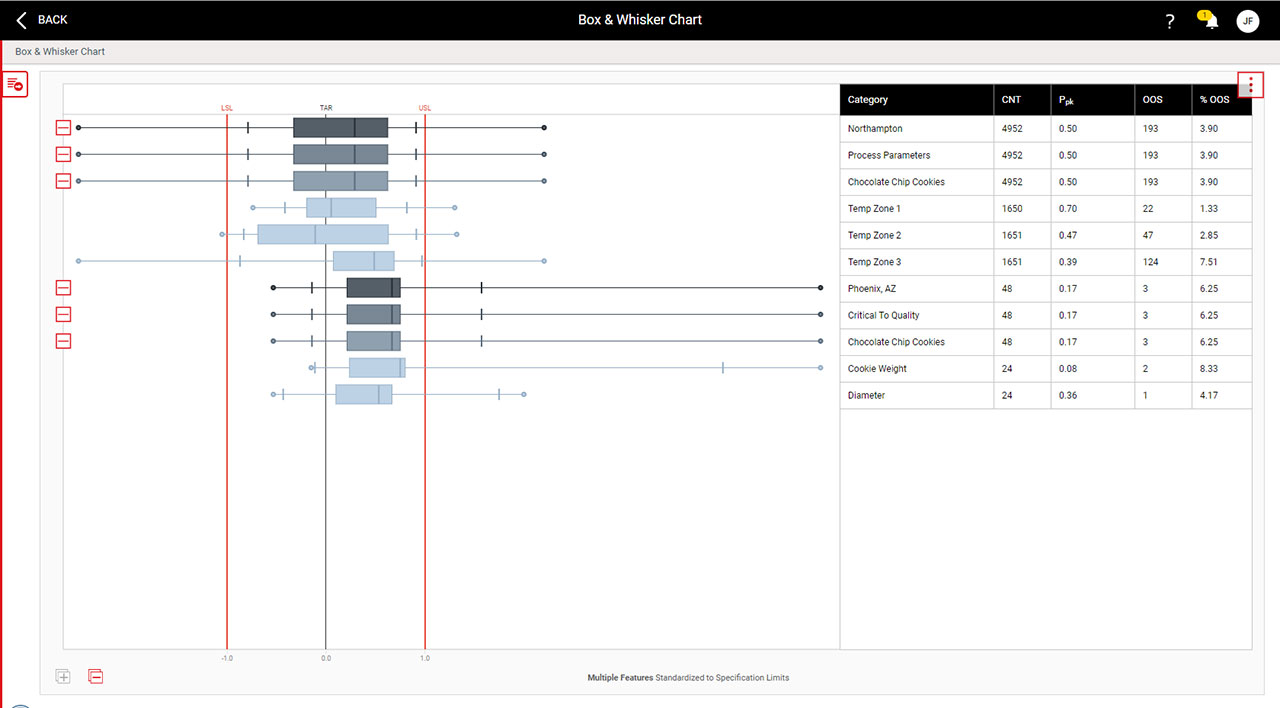
Compare quality data from multiple parts, lines, processes, shifts, sites, and more, so that you can cut straight to the heart of quality issues instead of drowning in individual charts graphs.
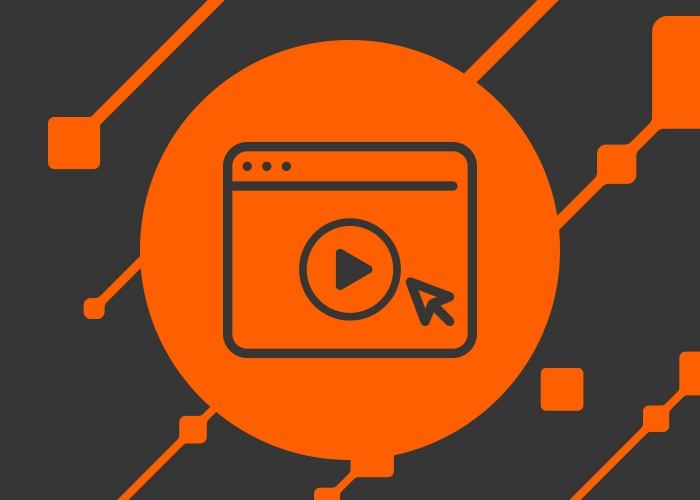
How do dashboards change the way people work?
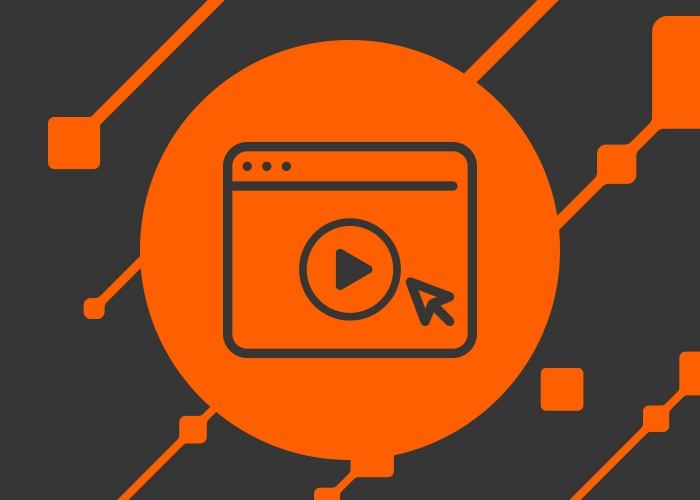
How does Enact help prioritize the greatest improvement opportunities?
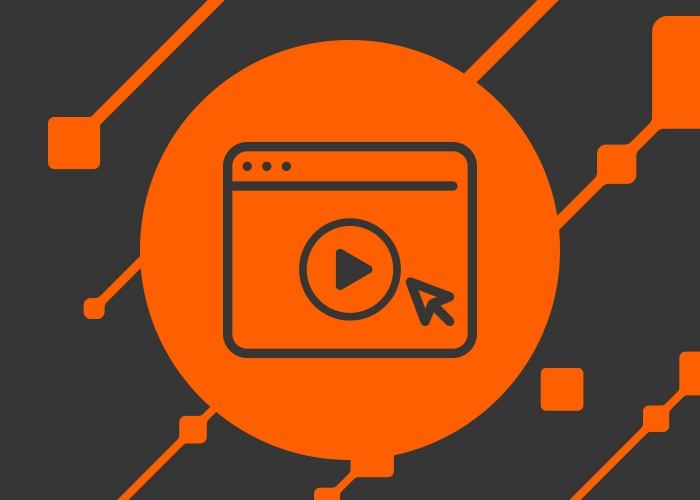
Enact: Favorite Features
Implementing SPC in Manufacturing Reduces Complexity
Complexity in operations can drive up manufacturing costs and frustrate manufacturing teams.
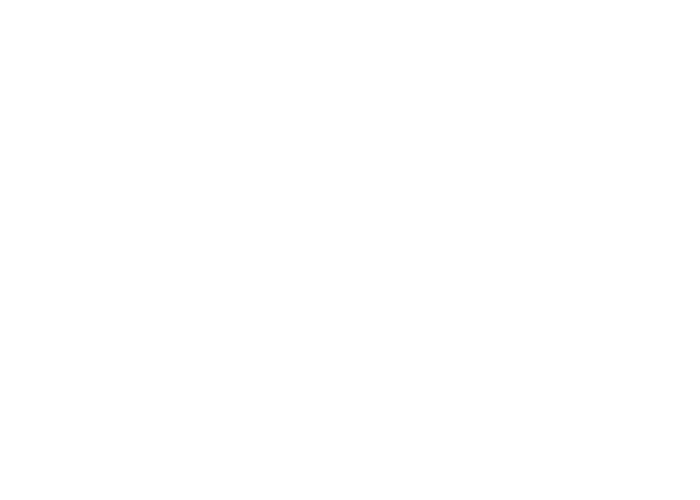
SPC DEMO
Don’t miss out! Book a demo of our specialized SPC software and unlock immediate improvements in your processes.
How Implementing SPC in Manufacturing Can Help
Complexity lurks in many corners of the manufacturing plant:
- Manual data collection processes that complicate later analysis (e.g., handwritten data that might be difficult to read, paper reports that can become lost or damaged)
- Lack of analytic capabilities that make attempts at quality analysis time-consuming and complicated
- Inconsistent processes that make it difficult to plan for quality improvements
- The introduction of additional or different steps across shifts, lines, employees, or sites
Using modern statistical process control for quality improvement helps to combat complexity by providing a means to understand and strategize around expected, standard variations in process quality.
Use Enact to Reduce Complexity
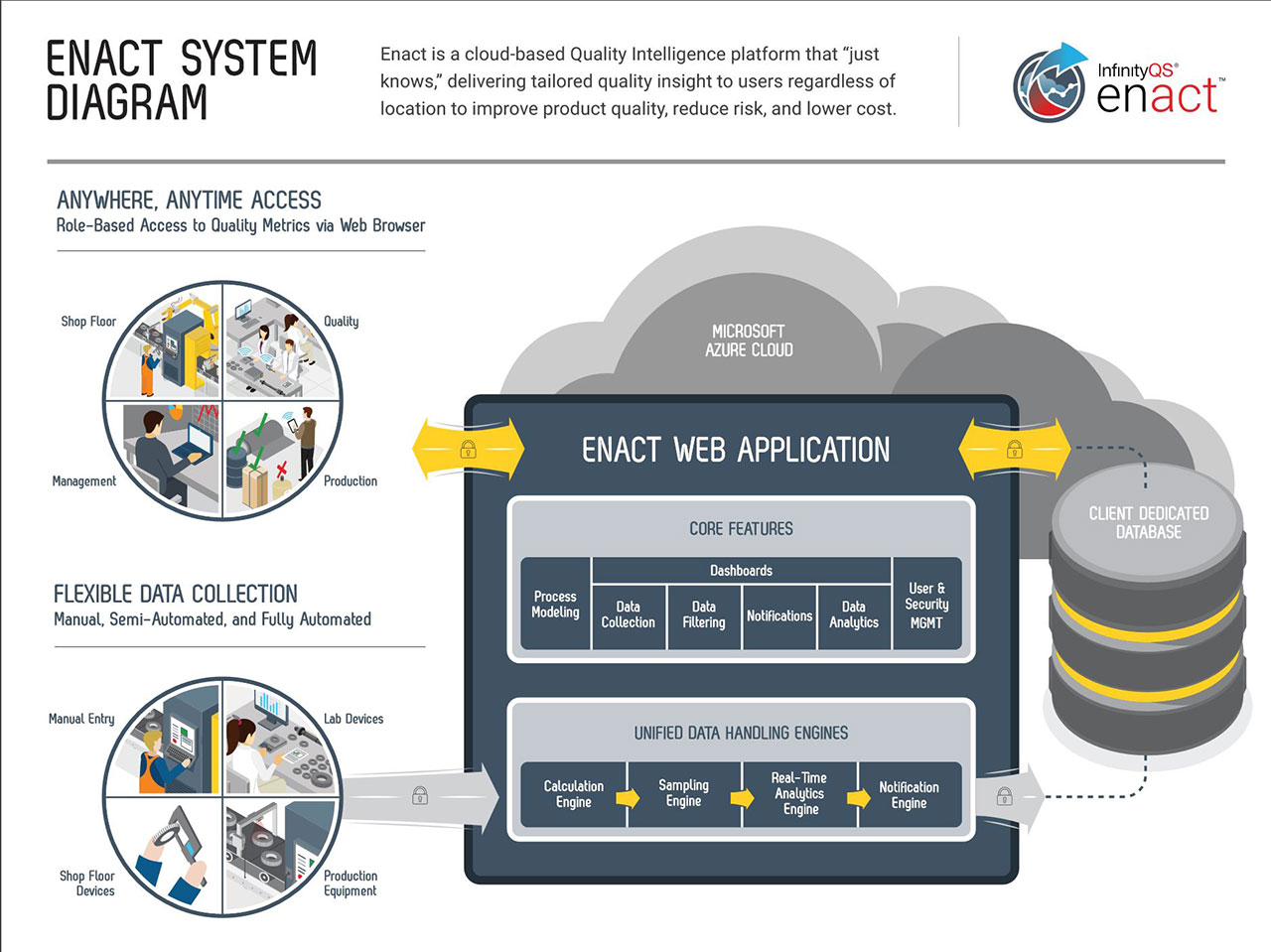
Many SPC quality systems promise to help improve processes—but then require extensive effort or additional expenses to integrate with existing infrastructure. Not so with Enact®, a cloud-based quality solution that is easy to try, use, and buy. Enact doesn’t require changes to your existing infrastructure, or the purchase of additional “modules” to achieve full functionality.
Enact can help your operations and quality improvement teams ramp up and start using SPC quickly, with intuitive UIs and extensive self-help. Not only does this reduce stress and slow-downs on the line, but your IT resources are also freed up for other tasks.
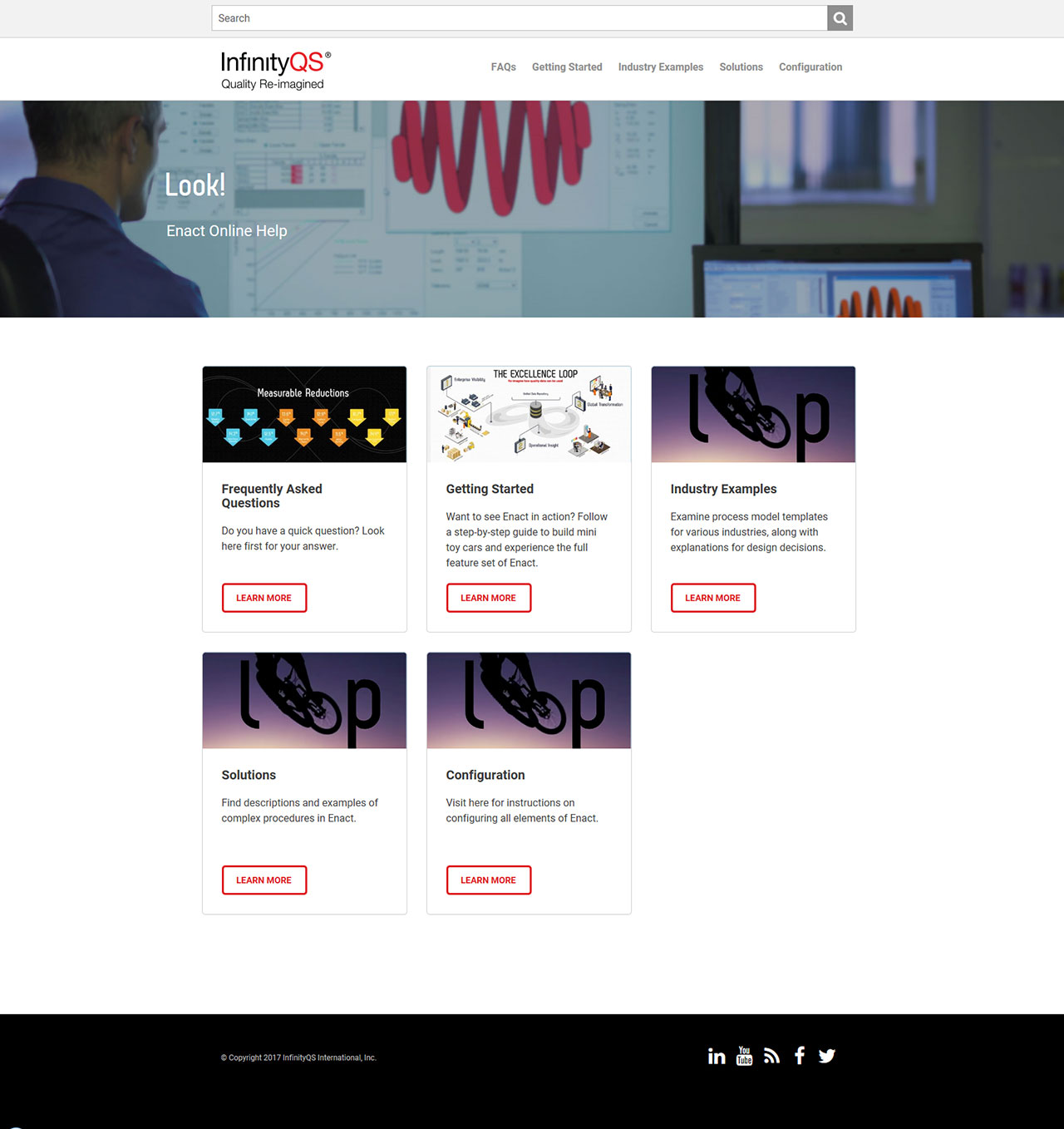
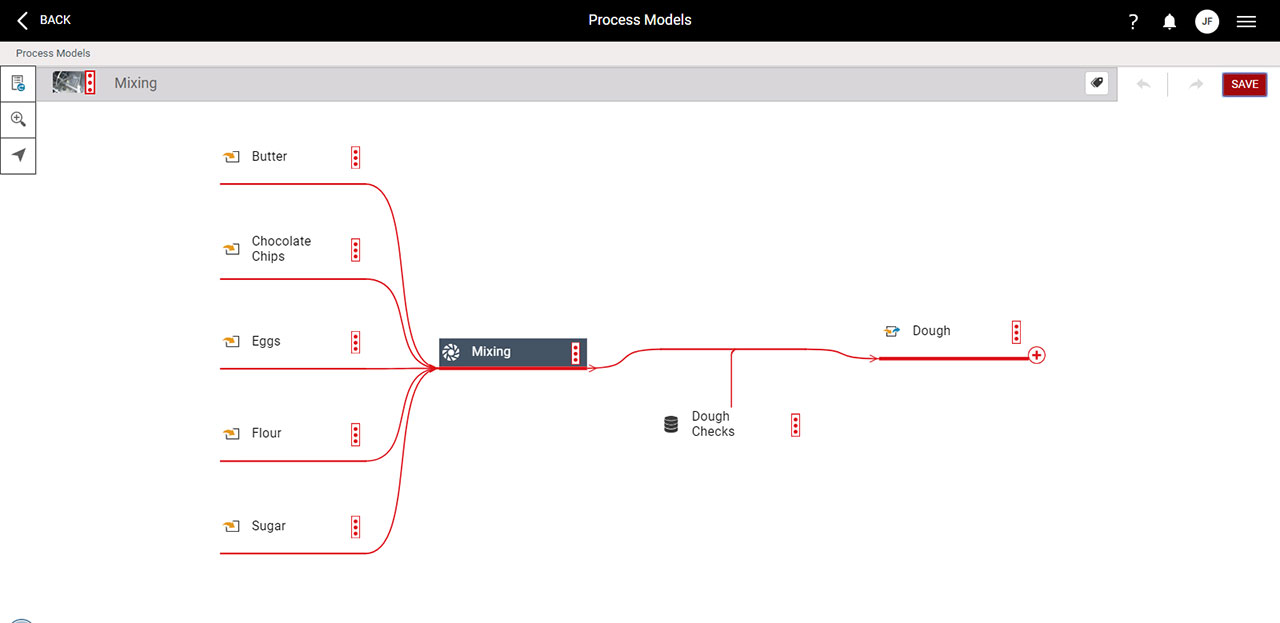
Enact uses process models and part recipes to provide a clear visualization of your manufacturing processes. With SPC that works like you do, you simplify the data collection process and reduce the burden on operators. Plus, this type of visual mode creates a reference that enables input from multiple sources and helps to clarify and streamline communication.
With Enact, you don’t need to jump through multiple hoops to see the “big picture” of manufacturing quality data. Customizable dashboards help cut down on complexity by showing you what you need, when you need it.
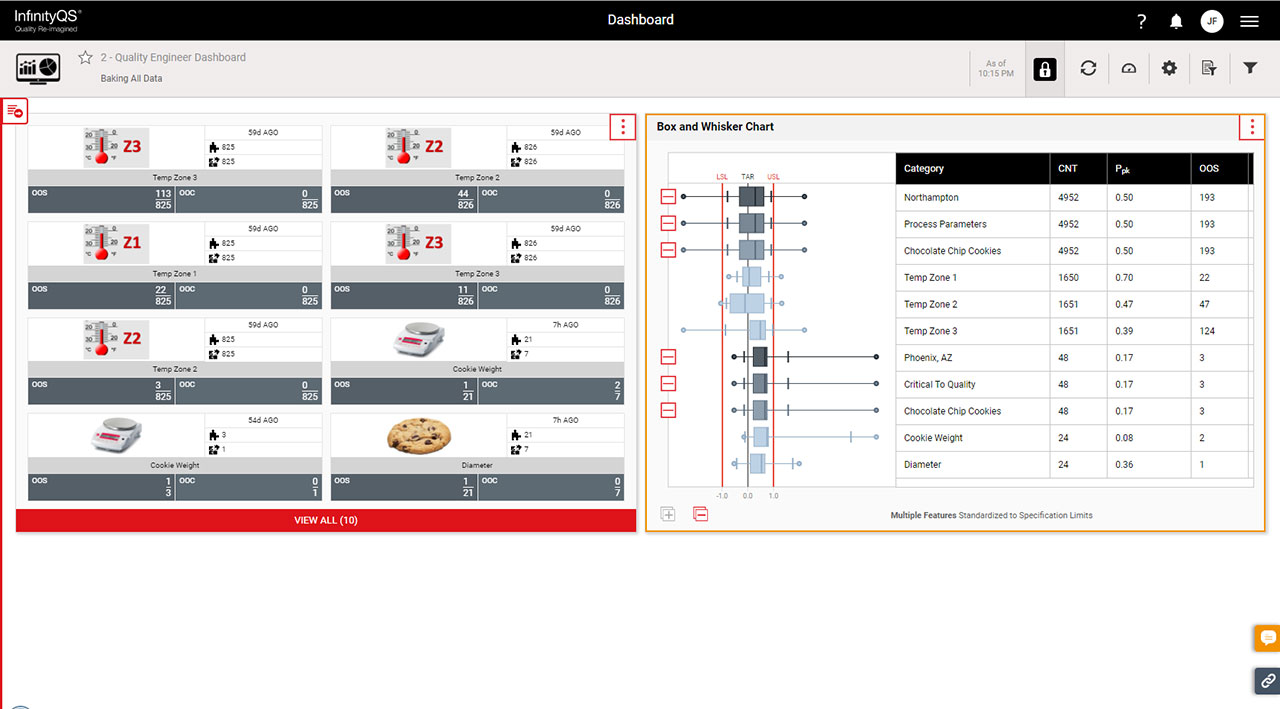
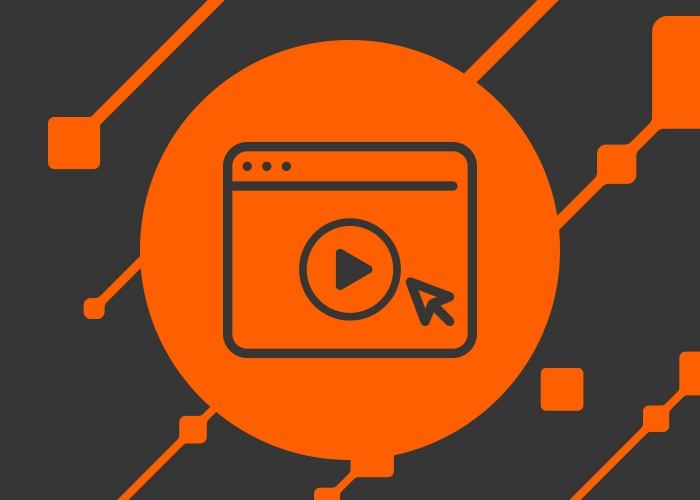
How does the Enact Process Model enable collaboration?
Speed Responsiveness to Customers and Auditors with SPC Tools
Audits can cost manufacturers thousands in lost time—and those are the ones that go right.
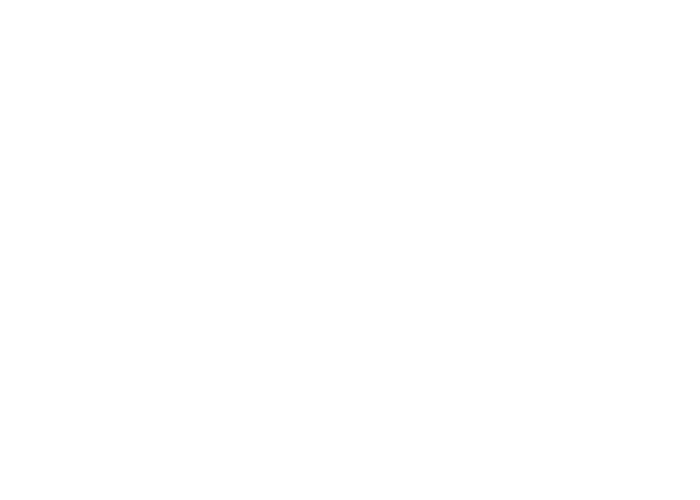
SPC DEMO
Don’t miss out! Book a demo of our specialized SPC software and unlock immediate improvements in your processes.
How SPC Can Help
For manufacturers, industry audits are typically a stressful endeavor. Depending on your industry, regulations and compliance issues can be complicated, overwhelming—and devastating, if not followed and documented correctly. With an audit on the horizon, it can be difficult to find the time to locate, compile, and present the requested data while staying on top of all your regular day-to-day tasks. A statistical process control (SPC) system can help ease the process, giving you a more efficient way to collect, store, and retrieve quality and operations data.
Use Enact to Make Audit Prep Easier
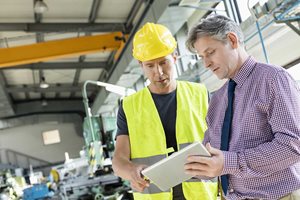
With Enact®, you can easily prove that checks were completed correctly and on time. You can create reports in minutes, pulling together quality, preventative control, and other data across one shift or multiple shifts on multiple days.
Easily create customized reports in response to specific auditor or customer queries (e.g., an exceptions report that shows only applicable alarms, events, assignable causes, and corrective actions).
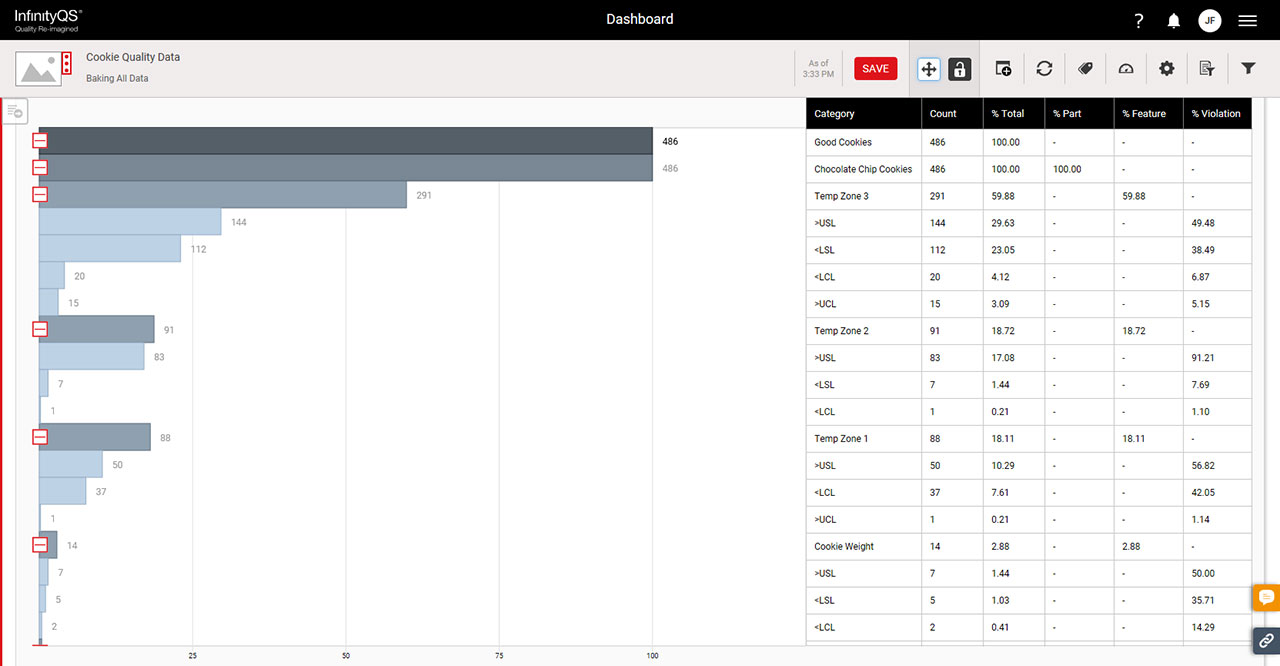
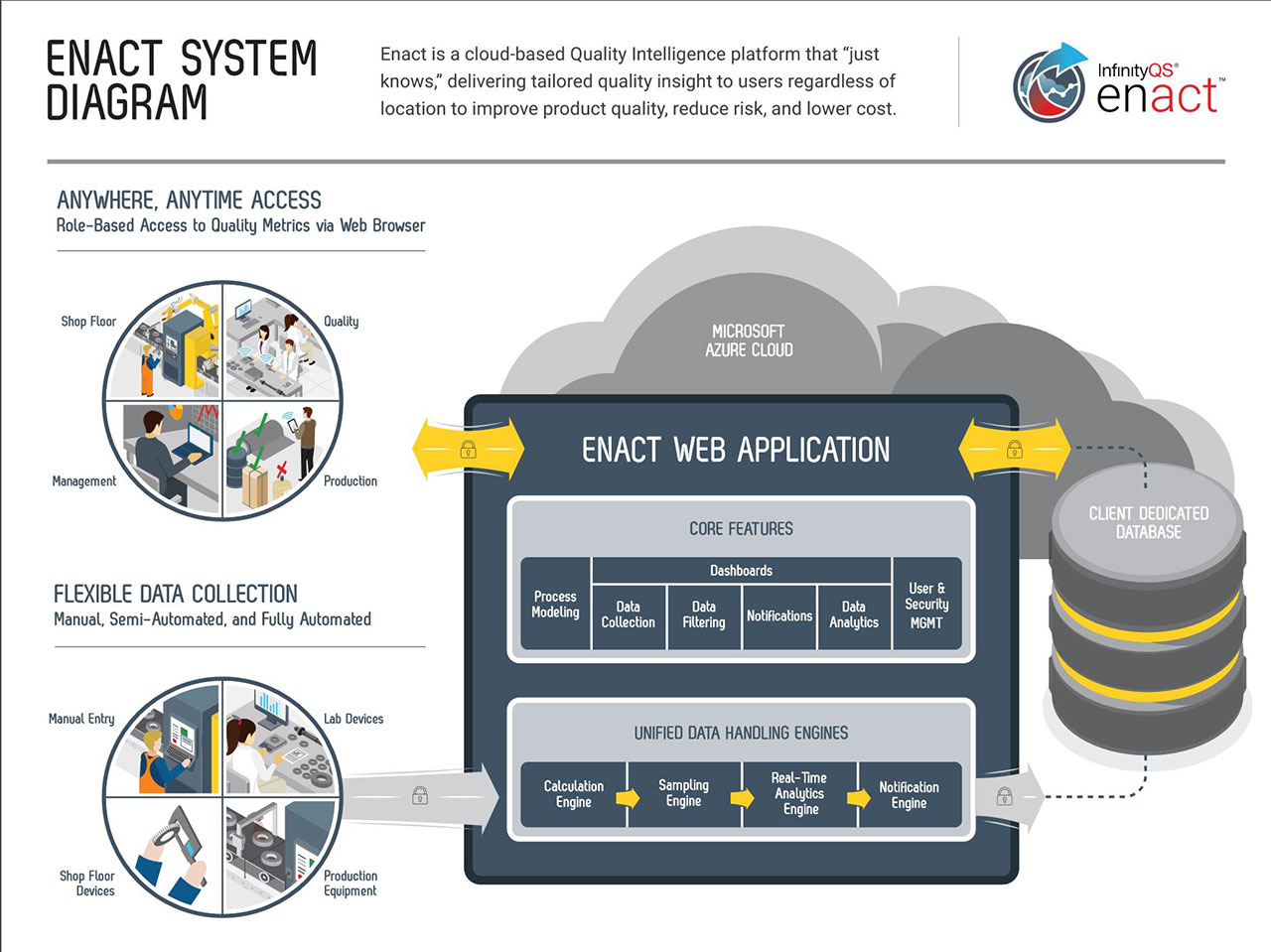
Save expensive physical storage space with Enact’s secure, cloud-based environment—without sacrificing anywhere, anytime access.
Improve traceability with Enact, for more precise tracking in the event of a problem with the quality of raw materials or finished product. Improved responsiveness in such situations can help to mitigate damage to your brand.
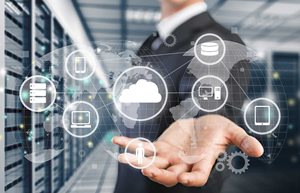
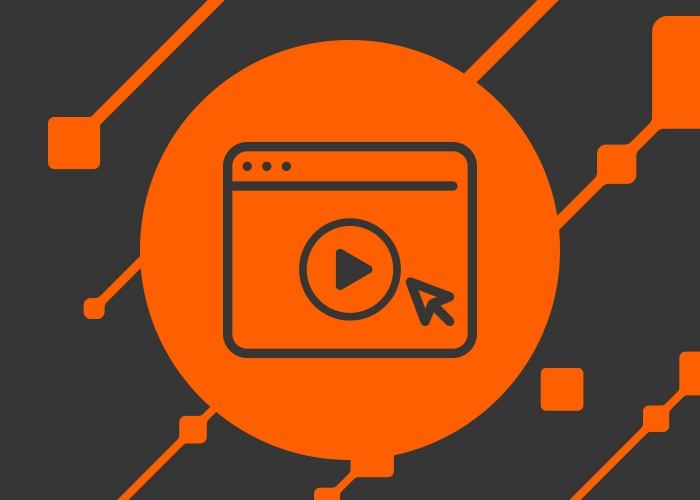
What is the Ultimate Value of Having Data Centralized
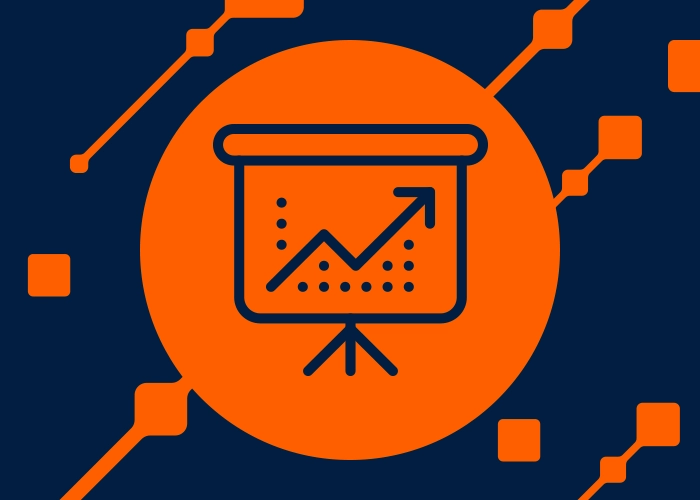
TEL NEXX
Improve Productivity with SPC
Inefficiency is the enemy of manufacturing profit.
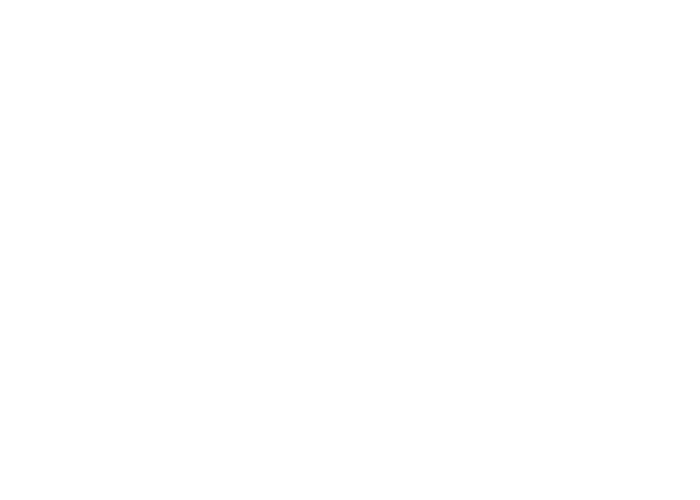
SPC DEMO
Don’t miss out! Book a demo of our specialized SPC software and unlock immediate improvements in your processes.
How SPC Can Help
“Time is money,” the saying goes—and nowhere is it truer than in manufacturing. Ideally, you can produce as much quality product as possible in the span of any given hour—without inefficient processes siphoning off the resulting profits. Many manufacturers see quality-improvement efforts as a cost center, when in fact they can help to increase profits by improving efficiency across the board and helping to—
- Reduce scrap and rework
- Minimize unplanned downtime
- Provide input or guidance for best practices
- Improve product consistency
Use Enact to Improve Efficiency and Productivity
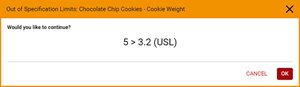
Enact® saves operator time by improving the efficiency of the data collection process, including the ability to pull in data from equipment that supports automated collection. Even for machines that require manual recording of data, entering that data directly into Enact is fast and easy. Plus, Enact supports the configuration of entry limits, so that any accidental typos or transpositions are easier to catch immediately.
Forget the hours and hours that many SPC systems demand when it comes to retrieving and analyzing quality data. With Enact’s Unified Data Repository, retrieving information, tracking trends, and responding to reporting, customer, or audit demands takes a fraction of the time other systems require.
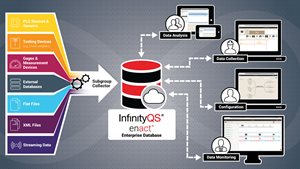
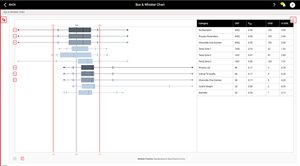
Unlike other SPC systems, Enact makes it possible to compare multiple products, shifts, processes—even sites—in a single chart. No need to export data for further calculations in Excel or Minitab; with Enact, you have robust, powerful analytic capabilities all from within your SPC system.
Thanks to Enact’s support for historical and aggregated analysis, you can more easily discover the approaches that lead to optimal quality. This ability supports the development of best practices, which can improve efficiency across your organization. And with Enact, you have the means to verify that such practices are being followed to the letter, across lines, shifts, and sites.
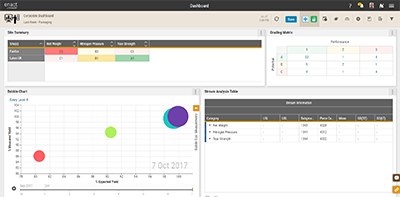
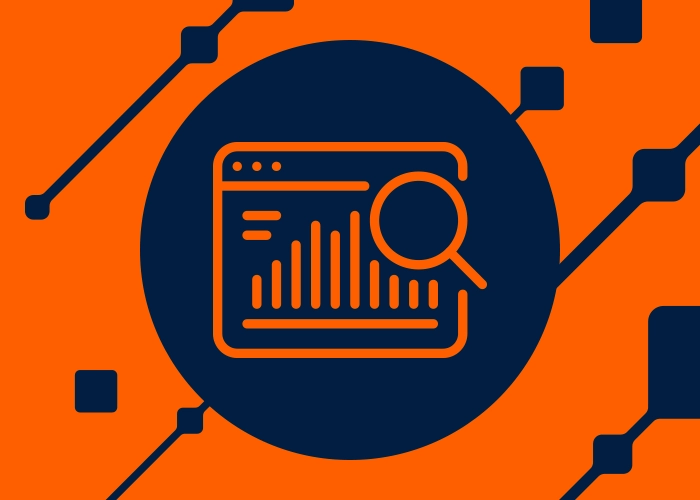
The Second Life of Data: Quality Analytics and Manufacturing Efficiency
Reduce Defects and Recalls
Non-conforming product can ruin your day, your reputation—and your manufacturing business.
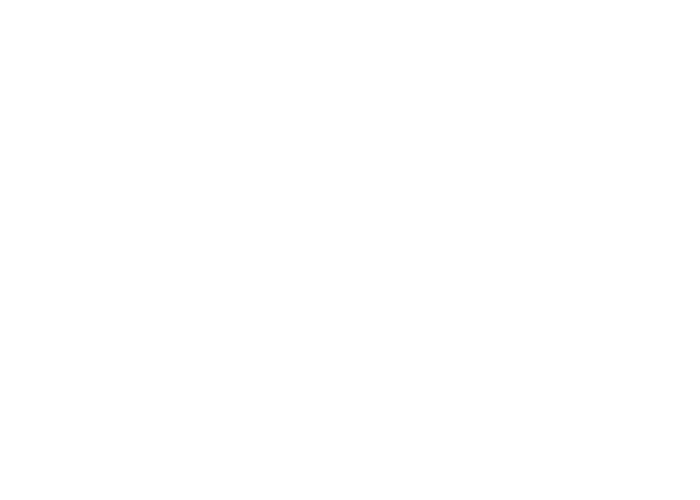
SPC DEMO
Don’t miss out! Book a demo of our specialized SPC software and unlock immediate improvements in your processes.
How SPC Can Help
The right statistical process control (SPC) solution can help you reduce or even eliminate the amount of defective product that comes off the production line—and thus the number of expensive recalls you must carry out. Recalls are costly in a multitude of ways:
- Product and material replacement costs
- Transportation costs
- Wasted employee hours
- Lost production time
- Loss of brand reputation
- Loss of customers
Use Enact to Reduce Defects and Recalls
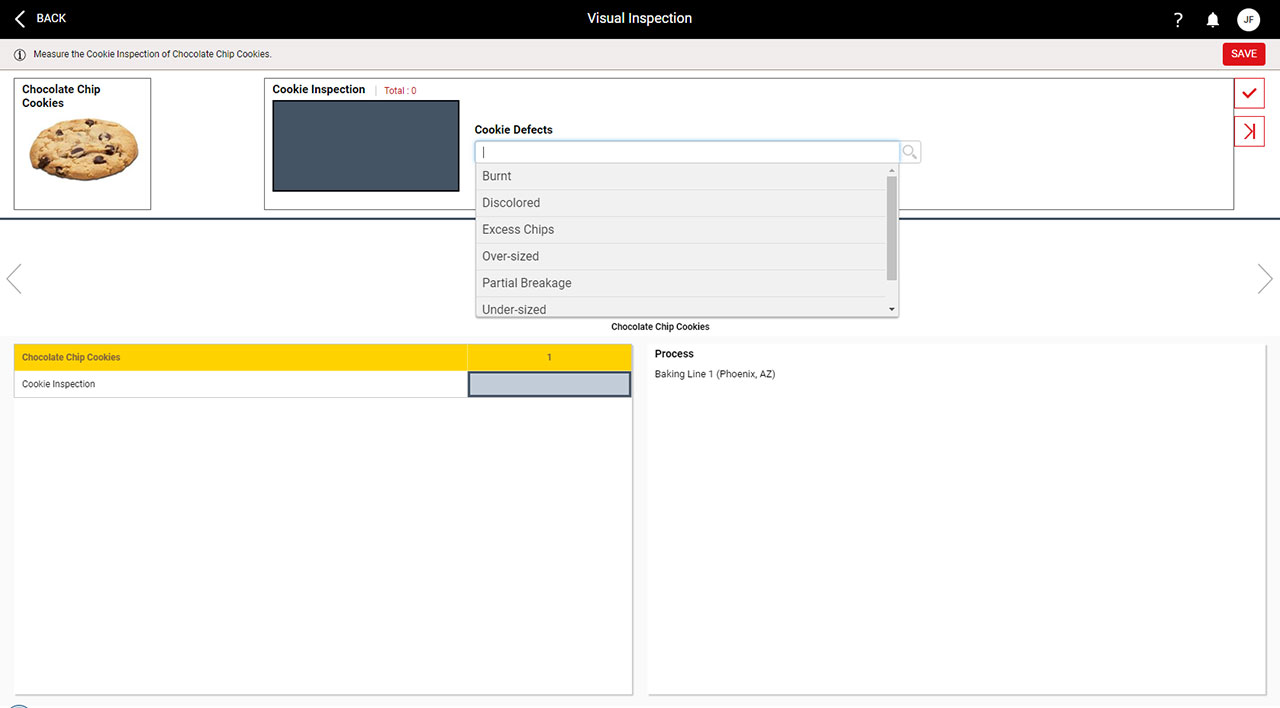
Many manufacturers track multiple types of defects, including visual defects. Collecting this data at various intervals for multiple products can become time-consuming. With Enact®, you can collect such data in just one data entry configuration, yet configure separate system alarms for each defect type.
Enact supports the collection, notification, and analysis of both defectives (i.e., pass/fail on items) and defects (i.e., condition count). Multi-level Pareto charts enable the display of defect codes, sorted and displayed by shift, customer code, employee, lot number, part, or any tagged descriptor.
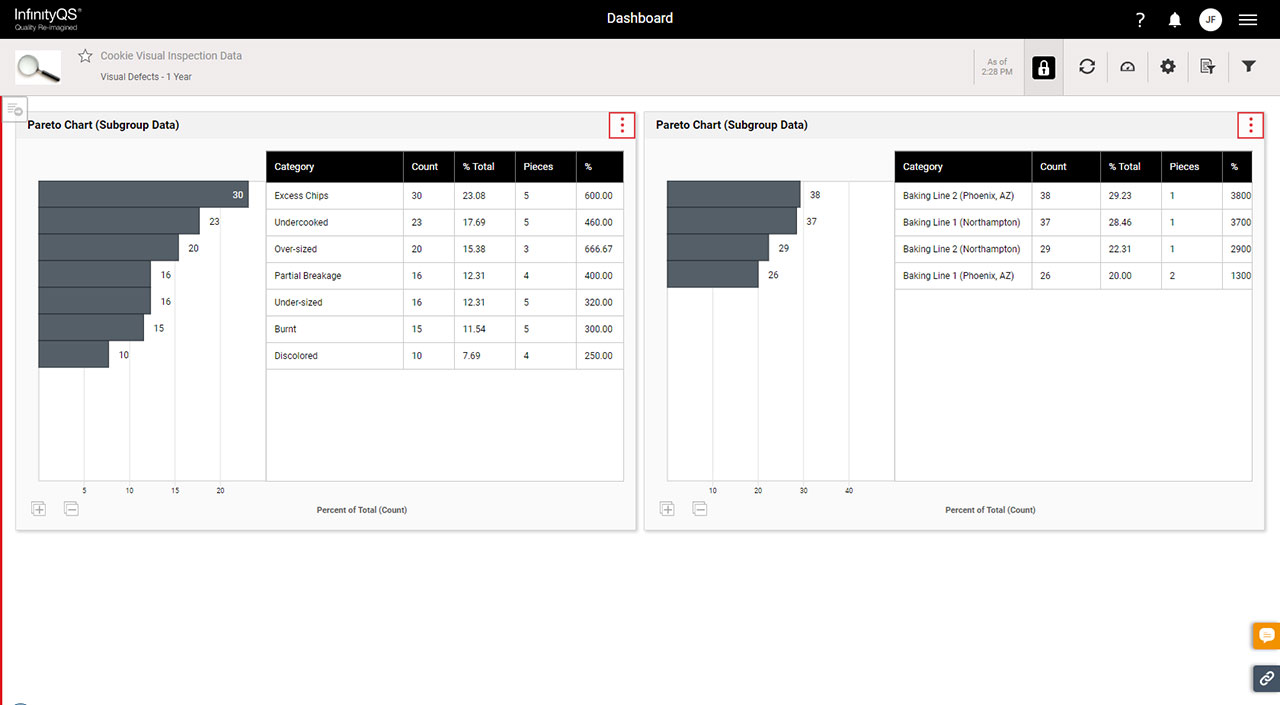
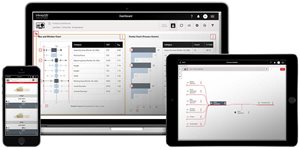
Further reduce defects by maintaining better traceability of raw materials. With Enact’s cloud-based, global, mobile capabilities, you can communicate and observe alerts and monitor quality from any location, 24/7.
Enact provides the precise, configurable data to support a Six Sigma implementation, helping your manufacturing organization extract optimal value from your quality data and reduce or eliminate defective products.
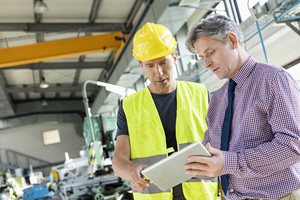
How to Reduce Waste in Manufacturing
Out-of-spec product can rack up losses. SPC enables waste management in manufacturing.
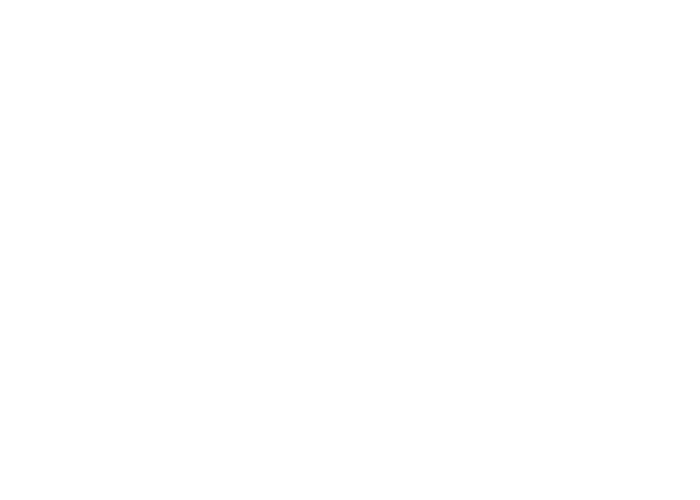
SPC DEMO
Don’t miss out! Book a demo of our specialized SPC software and unlock immediate improvements in your processes.
Reduce Waste and Scrap: SPC Can Help
A robust statistical process control (SPC) solution can reduce waste by helping your operations team spot critical out-of-spec dimensions. The earlier you catch such issues, the less wasted materials or recalled products you’ll need to deal with. InfinityQS SPC solutions provide the tools you need to catch process problems—fast. Together, we’ve helped our customers save millions of dollars in reduced waste.
Use Enact to Enable Waste Management in Manufacturing

You can’t stop waste if you can’t find it. Too many companies use guesswork to figure out why product isn’t up to snuff. But with Enact®, you can pinpoint how to reduce waste in manufacturing and significantly reduce costs throughout your operations.
When you test quality only at the finished product or final production stage, you can find yourself with staggering amounts of waste and scrap, in ruined product or rework time. Enact enables automatic notifications and staggered quality checks. That way, operators and quality personnel know immediately if a process, machine, or product falls out of spec—and can resolve the problem before it causes too much damage.
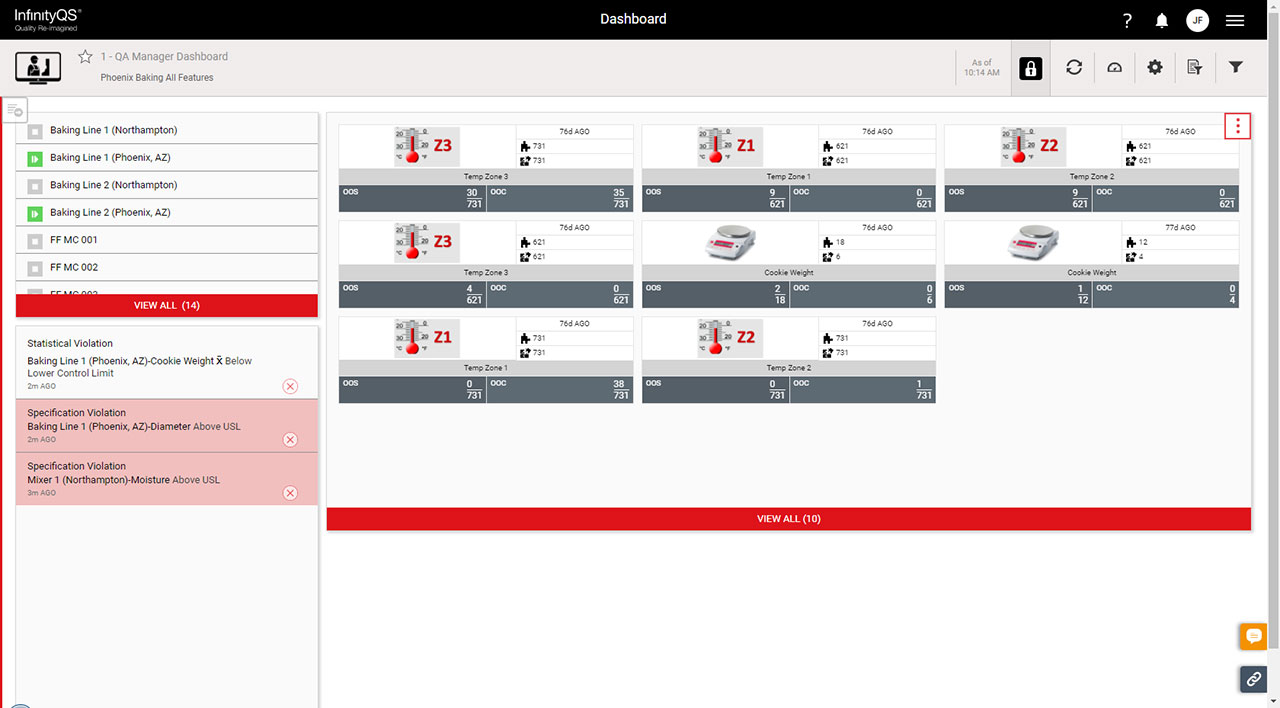
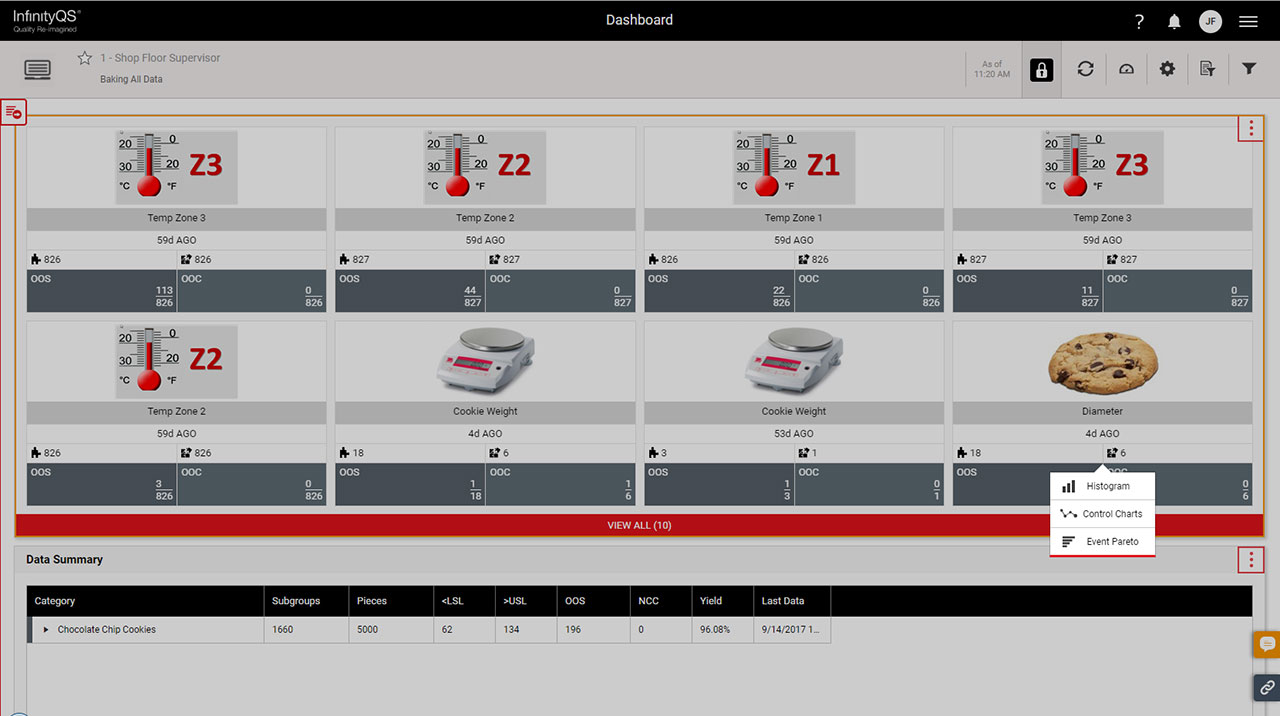
Enact enables a “big picture” view of whether processes are running smoothly or need attention. When you see trouble, it’s easy to drill down into the details of real-time SPC alerts and operations status, for better problem-solving and a faster resolution.
Fighting waste is a never-ending battle. With the power to roll up aggregated and historical data across processes, products, lines, and even sites, Enact gives you the ability to track trends and variations that lead to waste—even for processes and products that are within spec. As a result, InfinityQS customers have saved many millions of dollars.
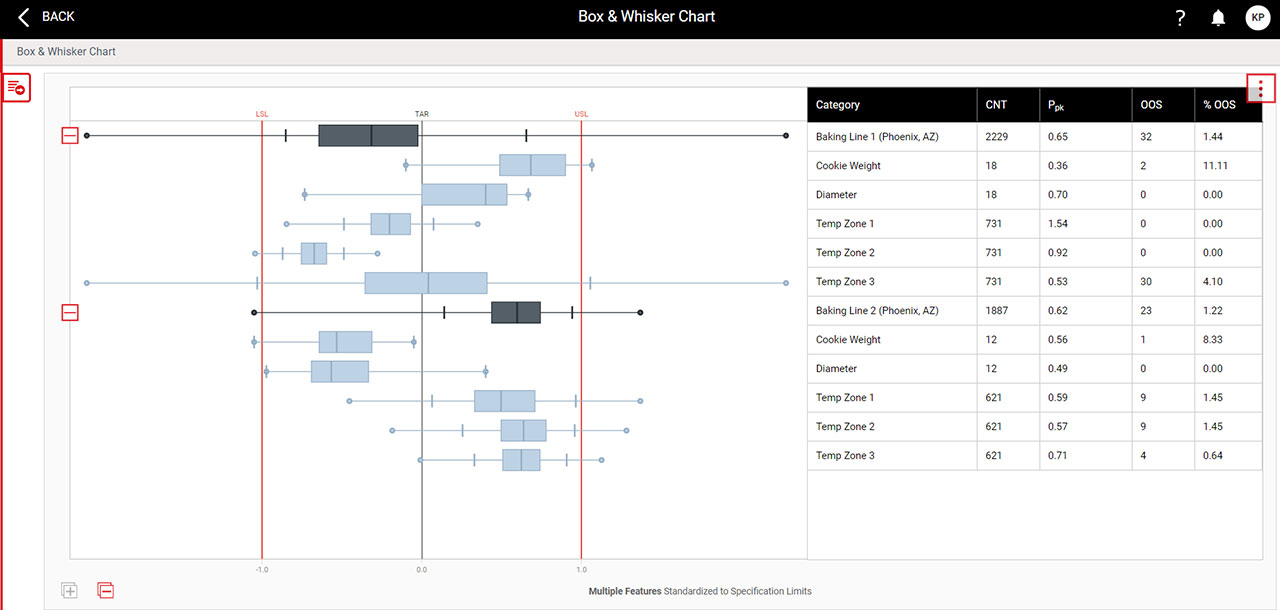
New SPC Tools for a New Era of Quality
Discover substantial benefits for your manufacturing organization when you modernize shop floor operations with new quality control tools and techniques.
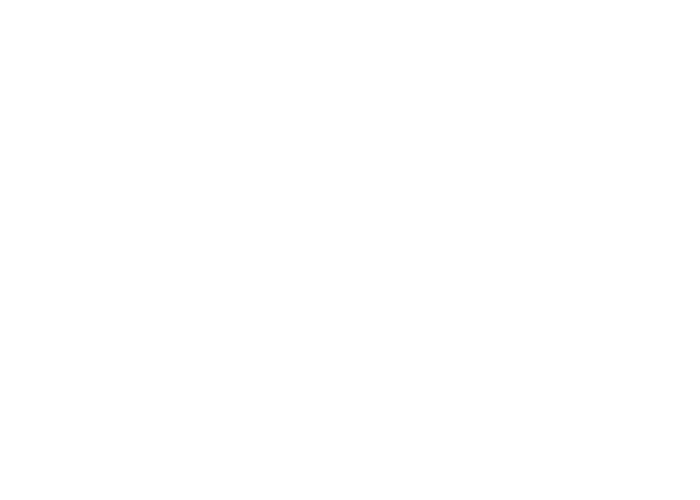
SPC DEMO
Don’t miss out! Book a demo of our specialized SPC software and unlock immediate improvements in your processes.
Embrace a better SPC solution
Manufacturing has changed. Yet many manufacturers still approach quality improvement and statistical process control (SPC) with yesterday’s mindset and SPC tools. Why not meet these challenges with solutions that work with today’s technology and data loads, rather than keeping you stuck in the past?
InfinityQS® software—ProFicient™ for on-premises or Enact® in the cloud—brings SPC tools up to speed. With features that help you optimize and modernize data collection, analysis, and reporting, our solutions enable you to overcome today’s most pressing problems and challenges.
Think you can’t afford an SPC solution?
With InfinityQS Enact, Frost & Sullivan’s Best Practices Award winner for Product Leadership, implementing SPC software has never been easier—or more affordable. From low cost of entry to robust help systems, Enact is designed to make statistical process control tools work for you. Plus, our team of Six Sigma green and black belts understand quality and are ready to provide the tools and training you need to become a model of modern manufacturing success.
- Starts at just $65/license/month
- Easy to learn and use from anywhere, anytime
- Cloud-based deployment and extensive self-help to reduce IT burden
- Supplemental training available onsite or at our training facilities
The cost of standing still
Can you afford not to improve your process quality? Not only does InfinityQS Enact break through traditional SPC price barriers, it enables additional profit potential simply by helping you update the way you deal with data.
Data Collection
Save operations resources with more effective and efficient data collection.
Data Analysis
Improve data analysis with extensive charting and comparison capabilities.
Data Reporting
Respond more quickly to information demands with easier, faster reporting and data access.
Easy to start. Easy to expand.
Enact empowers you to quickly realize the benefits of digital data collection and analysis. Start today with:
- Five Enact licenses: add more as needed
- Quick Setup wizard: your guide to configuring data collections
- Video tutorials and easy-to-use help: available in our Guided Learning Center
- Flexible expansion: reconfigure your licenses, add licenses, integrate with other manufacturing systems, and move to automated data collection—at any time
Mitigate Risk
Prioritize quality and process control to reduce regulatory compliance risks, customer complaints, and recalls.
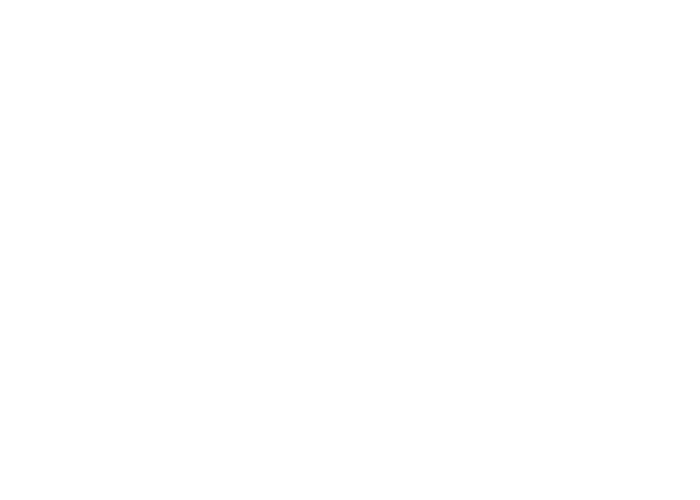
SPC DEMO
Don’t miss out! Book a demo of our specialized SPC software and unlock immediate improvements in your processes.
Prioritize Quality and Process Optimization to Protect Your Brand
InfinityQS® solutions use proven statistical process control (SPC) methodology to help you prevent problems—and the associated risks.
Boost ROI
From giving you the insight you need to monitor supplier quality to improving traceability and streamlining audits, InfinityQS solutions provide unbeatable ROI.
Protect brand equity
Consistency is a hallmark of brand equity. How can you ensure that customers get the same high-quality product from any manufacturing site, at any time? How can you detect potential quality problems as quickly as possible—or better yet, spot the warning signs and prevent the problems? InfinityQS solutions provide targeted yet extensive data collection and capabilities, automated alerts, and aggregated access to historical data so that you can produce a consistently excellent product that meets brand expectations.
Reduce customer complaints
Your customers demand high quality, reliable products. You need proven, efficient quality control methods to meet those demands. One faulty process can set back both production and customer loyalty. With InfinityQS, you get solutions that help you respond to customer needs—quickly, flexibly, and consistently.
Minimize recalls
Product recalls are costly, not just in lost time and wasted materials but also in the potential loss of customer confidence and brand reputation. InfinityQS gives you the insight you need to reduce defect levels, automate policy and procedure enforcement, and reduce scrap and rework—all of which can help to prevent the dreaded recall.
Measurable Results
Hundreds of InfinityQS clients responded to a survey we conducted, documenting savings in key metrics including scrap, rework, defects, cycle time, overtime, warranty claims, MRB/sorting, holds, escapes, data collection, reporting and recalls.
The average results are as follows:
- 12.7% Weekly Scrap Reduction
- 14.3% Man-hour Rework Reduction
- 14.1% Overtime Reduction
- 12.9% Defect Cost Reduction
- 13.6% Cycle Time Reduction
- 14.1% Warranty Claim Reduction
- 11.5% MRB/Sorting Reduction
- 12.5% Holds Reduction
- 10.7% Escapes Reduction
- 14.4% Data Collection Time Reduction
- 17.1% Report Time Reduction
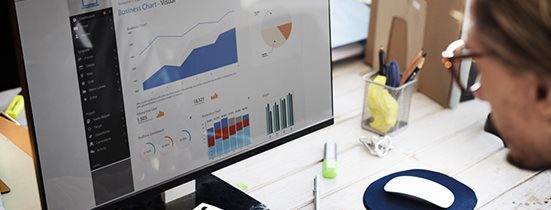
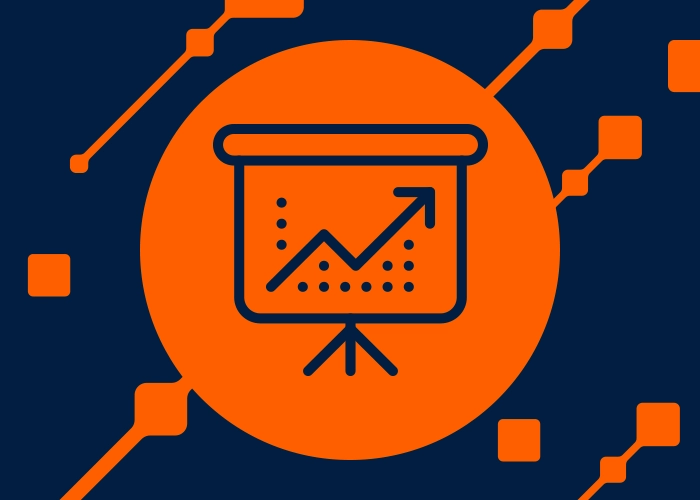
Elevating Quality to the Top Floor
Easy to start. Easy to expand.
Enact empowers you to quickly realize the benefits of digital data collection and analysis. Start today with:
- Five Enact licenses: add more as needed
- Quick Setup wizard: your guide to configuring data collections
- Video tutorials and easy-to-use help: available in our Guided Learning Center
- Flexible expansion: reconfigure your licenses, add licenses, integrate with other manufacturing systems, and move to automated data collection—at any time