Background
Polaris Industries of Roseau, MN is the nation’s largest manufacturer of light-duty all-terrain vehicles and snowmobiles, as well as Indian and Victory brand motorcycles. This world leader in off-road innovation continuously adds to its product offering to meet changing customer preferences. When preparing for introductions for new Slingshot® and RZR® vehicles, Polaris found that it needed to expand its supply chain for critical assemblies to include new vendors from around the globe.
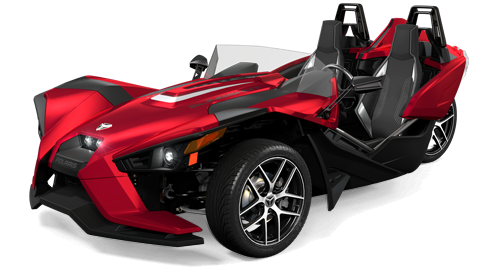
Issue
Polaris selected LifeStyle Metals Co. of Singapore to manufacture the fuel tank assembly for the Slingshot recreational 3-wheeled roadster. From the inception of the contract, Polaris began receiving out-of-spec fuel tanks that had to be rejected. This repeated pattern of returned product generated millions of dollars of cost overruns, as well as associated delays in assembly and, perhaps worst of all, delayed shipment of the final product to dealers.
Polaris risked being unable to meet the demand it had worked so hard to foster in preparing for the new product release. In order to avoid potential damage to the best-in-class Polaris brand, which could have a costly negative impact for years to come, Polaris needed to take action.
Vendor selection is a long, complex process, and once a vendor is in place, it is not easy to replace them. Often the supplier is the only option available for a special part. Because of this, Polaris had processes in place for supplier challenges. Polaris set LifeStyle Metals on a probationary program known as “Troubled Supplier Status” and threatened to cancel its contract with them if the unacceptable rejection rate continued. Though minimal improvements were realized, the number of refused fuel tanks for quality assurance failures was still too high.
Polaris partnered more closely with LifeStyle to help them raise the quality of their fuel tanks, realizing that without the visibility into supplier quality, significant improvements couldn’t be made. As supplier and customer worked together at the shop floor level to minimize quality failures, Polaris discovered the missing ingredient: insight into the Lifestyle processes to identify problems and implement corrective actions. Without this information, no amount of processes, disagreements, or even penalties would have addressed the problem.
Solution
The overall solution provided by PQ Systems has delivered easy data collection and analysis and seamless data sharing between plants. SQCpack helped them quickly pinpoint causes for out-of-spec product so that they could put corrective actions in place. This resulted in a significant decrease in out-of-spec product and allowed the manufacturer to maximize capacity across both plants.
By adopting SPC practices and leveraging SQCpack for the implementation, the manufacturer was able to run at maximum capacity, sold out capacity for several quarters, and is expanded with a third plant.
Outcome
The combined effort to communicate and improve quality with SQCpack led Polaris to gain trust and confidence in Lifestyle. LifeStyle Metals went from being a “Troubled Supplier” to shipping zero defects during a 6-month term. Polaris attributes this remarkable transformation almost entirely to the implementation of SQCpack, due to the software’s ability to facilitate better communication between customer and supplier, and promote greater accountability. SQCpack was so impactful that an expansion of SQCpack throughout the global supply chain at Polaris is in the planning stages. For Polaris, and all its suppliers, SQCpack delivers actionable and immediate results with easily justifiable ROI.
Retail sales for Slingshot moto-roadster “far exceeded the company’s expectations for sales and profitability,” in its first full year of availability. The highly successful Slingshot product launch helped ensure that Polaris remains a brand synonymous with adventure and passion.